November 29, 2022, © Leeham News: MTU and Pratt & Whitney presented an EU Clean Sky project today where they will develop an advanced engine concept based on the Pratt & Whitney GTF. The project is called SWITCH, an acronym for Sustainable Water-Injecting Turbofan Comprising Hybrid-Electrics.
There are participants from 11 countries in the project, among them Pratt & Whitney’s sister company Collins aerospace, GKN’s Swedish part, and Airbus.
The engine, which has a mild parallel hybrid architecture, extracts more energy from the turbofan fuel by driving the core exhaust through a vaporizer and then a condenser to recover the water in the exhaust gases, Figure 1. The water is then routed via the vaporizer through a steam turbine that co-drives the fan and is finally injected as steam into the combustor.
The WET cycle will gain about 10% efficiency compared to today’s GTF. The concept also has a hybrid part which is primarily used for a low-emission taxi.
The SWITCH engine
The SWITCH project is a European Clean Sky project with several participants, Figure 2. MTU, as a European company, is the lead. In total, Industry partners and Universities from 11 countries are involved in the project.
The first part, between 2023 and 2025, develops the WET engine components and further develops the hybrid technologies that Pratt & Whitney/Collins worked on in the STEP project and the regional turboprop demonstrator with De Havilland Canada.
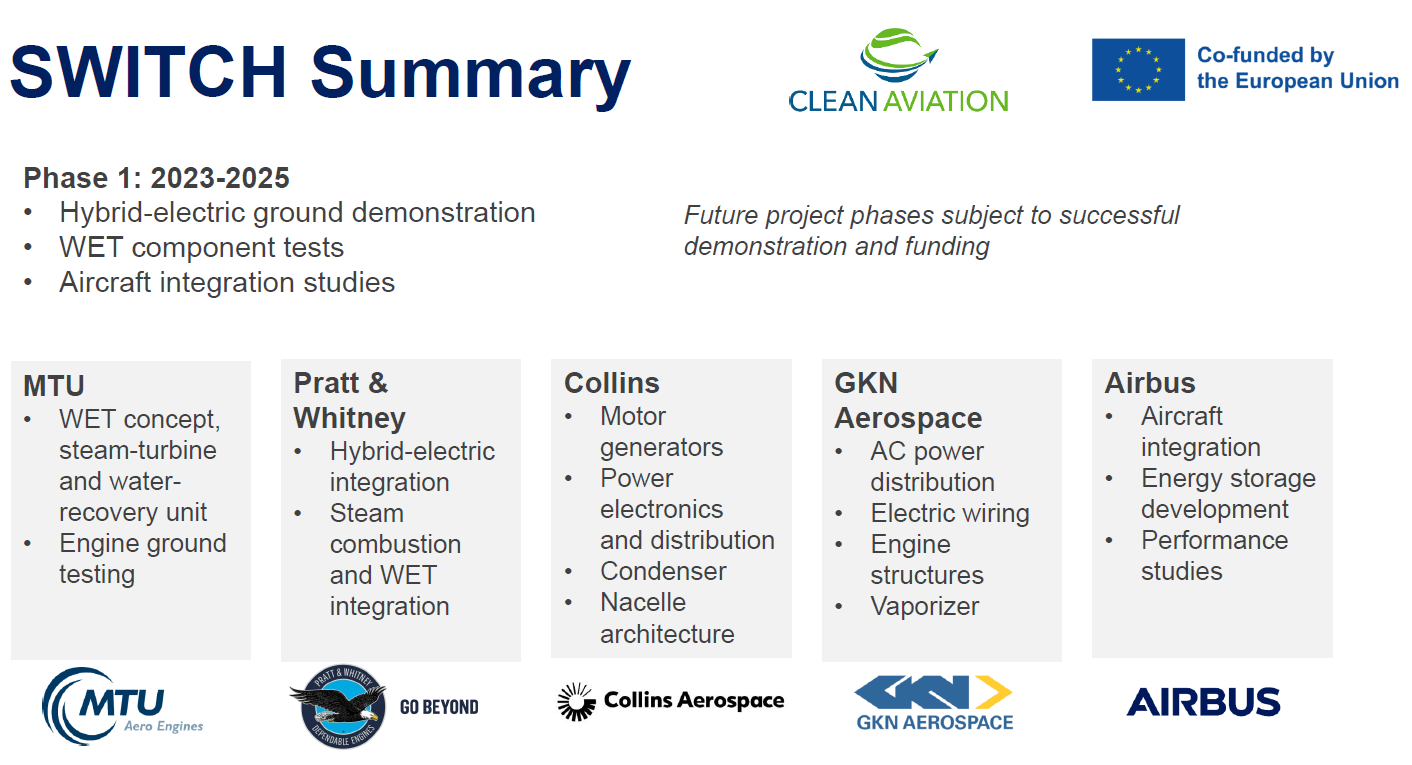
Figure 2. The SWITCH principal project members and the goal for Phase 1 of the project. Source: SWITCH.
The main innovation in the project is the WET engine principle that uses the water created in the combustion process of a gas turbine to enhance engine efficiency. The water in the combustion gases is routed to Condensors placed in the bypass stream, where the water is condensed and extracted, Figure 3.
The water is then routed to the Vaporizer, where the heat from the core exhaust converts the water to steam that drives a Steam turbine attached to the low spool of the engine. The core’s remaining heat in the exhaust is thus used to add power to the low spool and the fan.
After the steam turbine, the water is routed to the combustor as steam, where it’s injected to lower the combustion temperature. The lower combustion temperature reduces NOx creation by up to 80%. The mass increase from the water gives the combustion gasses a higher energy level so that more power can be extracted from the turbines.
The concept also lowers contrail generation as the amount of recirculation can be managed, and any excess water can be dumped into the atmosphere after the condenser.
A mild hybrid
The hybrid part is an add-on energy conservation part. During the ground stop, batteries in the fuselage are charged. The energy is then used to drive the fan via a motor generator working in parallel on the low spool, Figure 4.
The taxi and takeoff will consume the energy stored in the aircraft battery; therefore, the function during the rest of the flight is to assist the engine during power changes (by allowing more aggressive scheduling of the compressors) with the remains of the battery energy.
The assistance during takeoff is modest as the spool powers are north of 20MW each in this phase, and the motor generators are 1MW (low spool) and 0.5MW (high spool).
At cruise, the spools need between 5 to 7 MW each, dependent on the engine variant. The motors could then contribute up to 20% of the booster/fan shaft power, but I see no chance of having batteries with enough energy so these can contribute in these phases.
We need a minimum 1,000 kWh battery for taxi and takeoff, and it would weigh about 4t, so a battery that would have energy for climb and cruise is out of the question (it would weigh more than the whole propulsion system).
Couldn’t the gas turbine charge the battery via the motor generators? Yes, but as discussed several times, charging a battery with the aircraft’s gas turbines make little sense. You add over 10% of losses in the chain generator-power distribution-battery-power distribution-inverter-motor-fan compared with driving the fan directly.
In effect, the hybrid then increases the fuel consumption and CO2 emissions for the aircraft compared with using the gas turbine to do the job directly.
Aircraft integration aspects
The hybrid part requires a power distribution system in the aircraft and a propulsion battery, Figure 5. Airbus is looking after the integration aspects of these parts of the project.
The mass of the GTF engines would increase from 3t to about 4.5t when WET is integrated. So the engine mass goes from 6t to 9t. The hybrid part adds another 5t to this figure, dependent on the battery size.
Energy efficiency and emissions
The WET technology is projected to save about 10% of fuel consumption and, thus, CO2 emissions. It also lowers the NOx emissions of the engine by about 80% and reduces contrail generation.
The ambition of the project is to save up to 25% fuel and, by it, CO2 emission compared with today’s GTF turbofan that powers the Airbus A320/A321.
Where the other 15% comes from is for the project to explain. It can’t come from a hybrid part that is active during taxi (where it provides all necessary fan power) and takeoff, where it contributes about 5% of the needed power to drive the compressors and fan.
Conclusion
The WET engine concept is an interesting idea, equally applicable to Jet-A1, SAF, or hydrogen-burning engines.
What about the hybrid part? It makes sense to include it in a research project where the technology can be brought forward and knowledge gained. As presented, it doesn’t make sense for a serial application.
Related